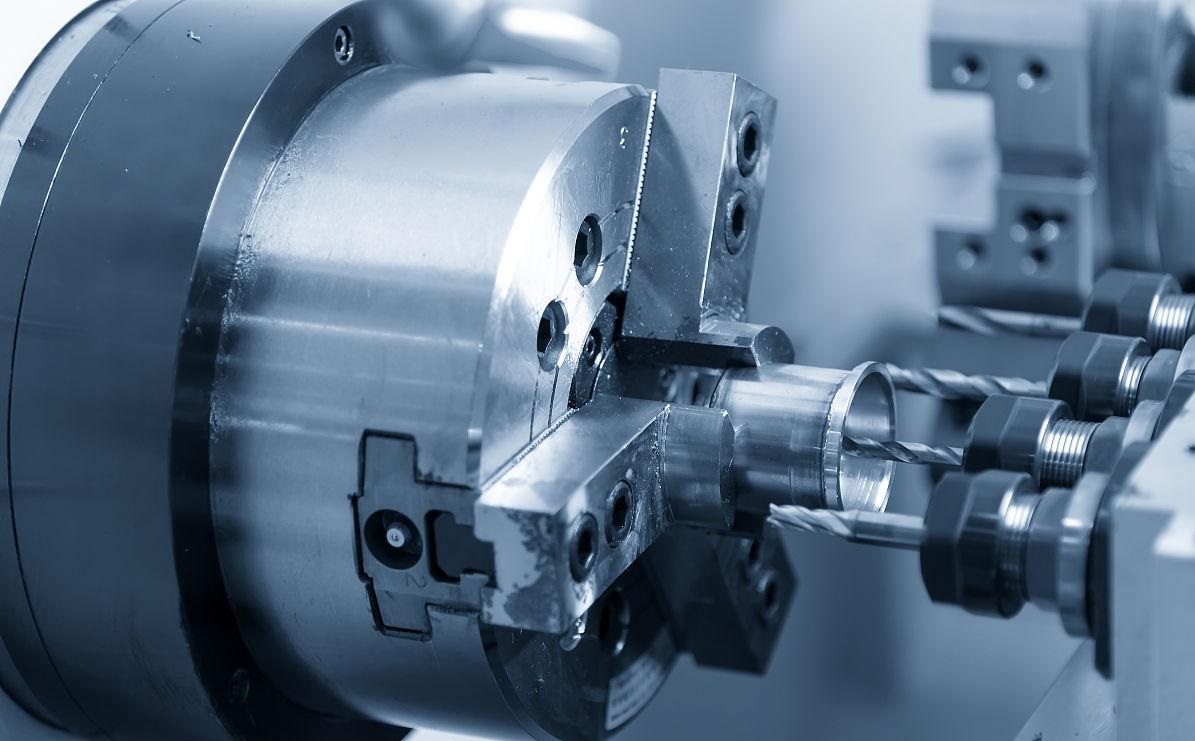
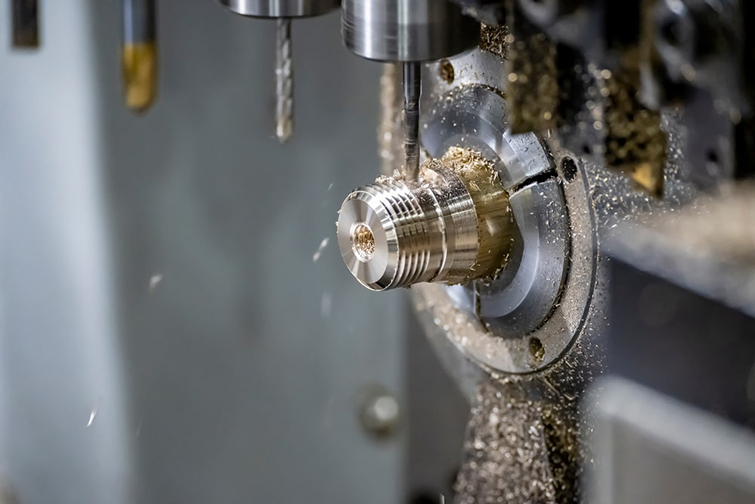
What Factors Impact Machining Tolerances?
When designing a part, engineers must establish machining tolerances early in the process. These tolerances ensure that parts are manufactured within acceptable dimensional variations. Several critical factors influence these tolerances, which affect both the machining process and final product quality.
●Material Properties
The material being used plays a significant role in determining the appropriate machining tolerance. Different materials behave uniquely under stress, and some are easier to machine than others. Here are the key material factors to consider:
▶Abrasiveness: Highly abrasive materials like glass laminates or phenolics can wear down cutting tools faster, affecting accuracy and tolerances.
▶Hardness and Rigidity: Softer or more flexible materials like polyurethane or XPS foam may require looser tolerances as they are harder to machine with precision.
▶Heat Stability: Machining generates heat, and materials like plastic can deform, requiring special handling to maintain precise dimensions.
Machining Methods
The type of machining process used has a direct impact on achievable tolerances. Certain methods allow for high-precision results, while others are more suited to general applications with looser tolerances.
Below are some common machining processes:
◆CNC Screw Machining: This method provides high precision, often achieving tolerances of ±0.005". It’s ideal for hard materials like phenolic and plastic that require strict dimensional accuracy.
◆Shear Cutting: Involves applying force to alter material dimensions. It's cost-effective but not ideal for soft or brittle materials, as it can cause failure.
◆Steel Rule Die Cutting: A more affordable method for cutting foam, rubber, and plastic materials. However, this process may not be suitable for very brittle materials that could crack under pressure.
◆Rail Cutting: A manual method that requires more flexibility in tolerances, often around ±0.031", due to its reliance on operator precision.
●Plating and Finishes
Finishing processes like plating can add material to a part’s surface, which may slightly alter the final dimensions. To ensure accuracy, these processes should be factored into the tolerance design before production begins. Failure to do so could result in parts that don’t meet the required specifications.
●Cost Considerations
Higher precision often comes at a higher cost. Parts with extremely tight tolerances, such as those requiring four or more decimal places, generally take longer to machine and require specialized equipment. For parts that don’t need such exact precision, looser tolerances can save both time and money without compromising quality.
By understanding the factors that affect machining tolerances — including material properties, machining methods, and costs — engineers can make informed decisions to produce parts that meet both functional and economic requirements.