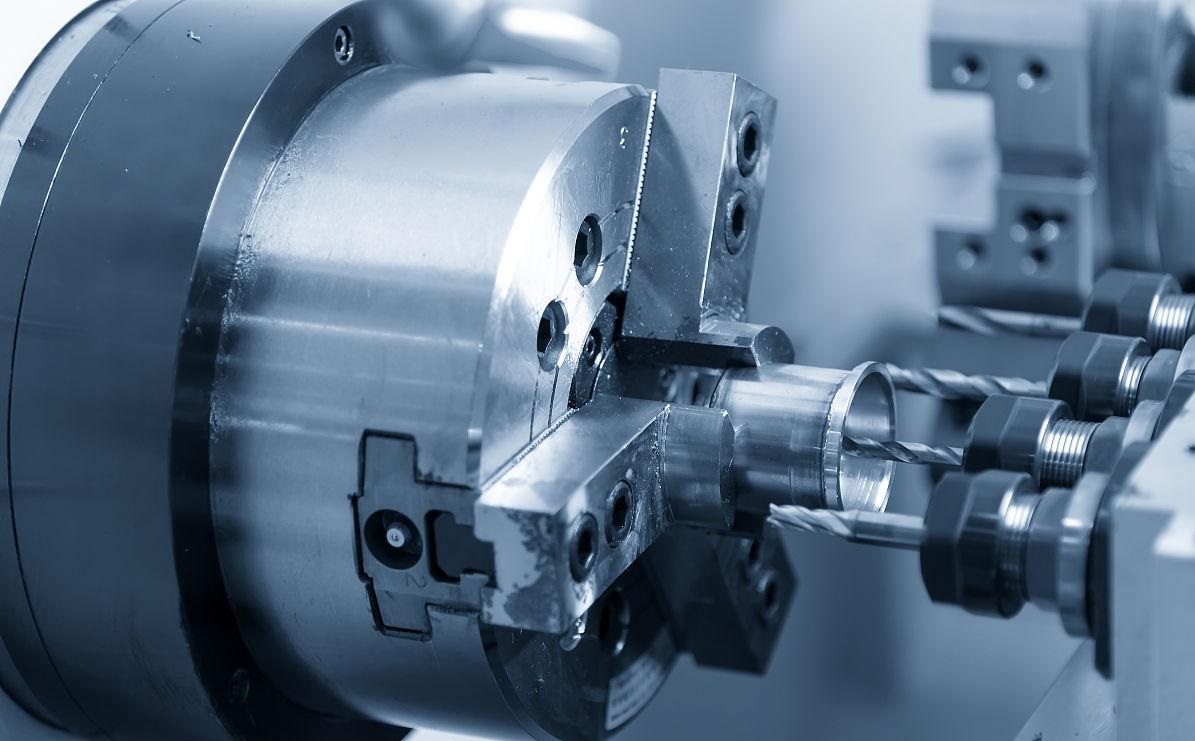
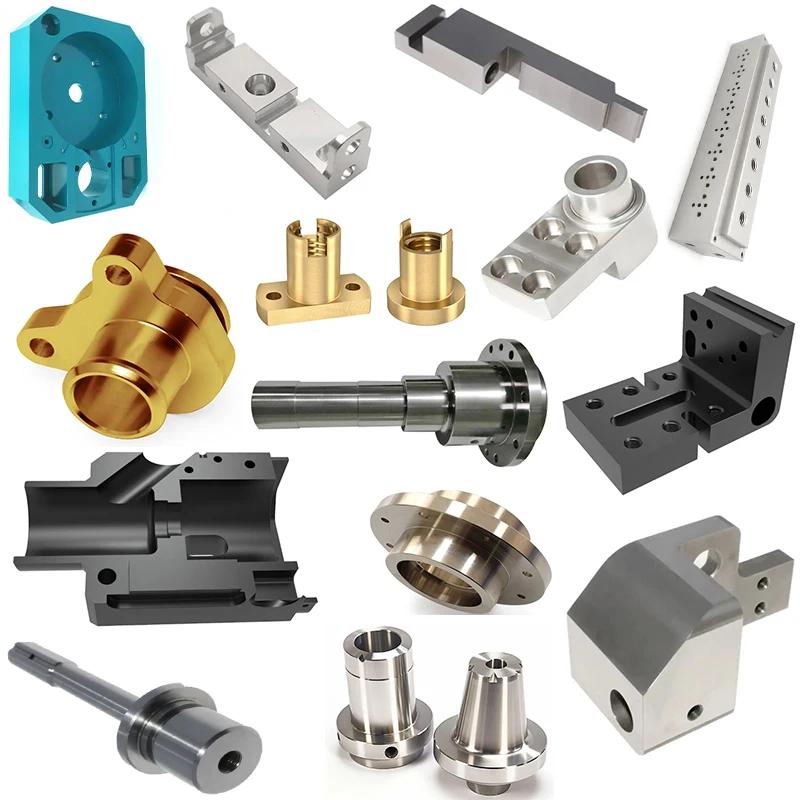
Do You Know the CNC Milling Surface Finishing Options?
When it comes to CNC milling, selecting the right finishing option is essential to meet both functional and aesthetic needs. From basic "as-machined" finishes to more specialized processes, each finishing technique can significantly affect the final outcome. Here's a look at some common CNC milling finishing options and how they can benefit your parts.
The Simplicity of "As Machined" Finishes
For many prototypes and functional parts, an "as-machined" finish is sufficient. This means the part is produced directly from the CNC milling process, without additional steps for smoothing or polishing. The resulting surface typically has tool marks, and the standard roughness is around 3.2 μm. However, a finishing pass can reduce this roughness to 1.6, 0.8, or even 0.4 μm. Keep in mind that adding finishing steps will increase production costs, but it can yield tighter tolerances.
In addition, while "as-machined" parts can sometimes be polished further, doing so can remove material and potentially affect the part's tolerances. Nevertheless, this finish offers some of the tightest dimensional accuracy compared to other options.
Bead Blasting for a Refined Surface
For parts requiring a more refined appearance, bead blasting is a great option. This technique uses small glass beads that are blasted onto the surface under high air pressure, effectively smoothing the part and eliminating tool marks. Bead blasting results in a satin or matte finish, giving the part a more polished look.
However, if your part has critical features like holes with tight tolerances, it's important to mask those areas to preserve the dimensions. This process can improve the part’s aesthetics without compromising its functionality.
Powder Coating for Enhanced Durability
If protection is a priority, powder coating offers an excellent solution. In this process, a thin layer of durable polymer is applied to the part, creating a corrosion-resistant surface. This finish is especially useful for parts exposed to wear and environmental factors. Powder coating is compatible with various metal materials and can be combined with bead blasting to create a smooth, matte finish.
Powder coating involves electrostatically spraying dry powder onto the part, followed by curing in a high-temperature oven. This process not only enhances durability but also allows for a wide range of color options, making it ideal for both functional and aesthetic applications.
Anodizing for Protection and Color
Anodizing is another CNC milling finishing option that provides both protection and aesthetic appeal. This process creates a ceramic-like surface layer that is highly resistant to wear, corrosion, and UV damage. Anodizing also offers the added benefit of a variety of color options, making it popular for both decorative and functional parts.
Anodizing is only suitable for aluminum and titanium alloys. The process involves immersing the part in a sulfuric acid bath, then applying an electrical current, which converts the metal surface into a hardened oxide layer. There are two types of anodizing:
- Type II (Decorative Anodizing): Produces a smooth, colorful finish with a thickness up to 25 μm. This type offers good corrosion resistance and is often used for decorative purposes.
- Type III (Hard Coat Anodizing): Creates a thicker coating (up to 125 μm) for superior wear and corrosion resistance. This makes it ideal for parts that need to withstand harsh conditions.
Conclusion
The CNC milling finishing process you choose depends on your part's requirements. Whether you need the precision of an "as-machined" finish, the refined appearance of bead blasting, the protection of powder coating, or the durability and aesthetics of anodizing, each option offers unique benefits. Understanding these finishes helps ensure that your parts meet both functional specifications and aesthetic desires.