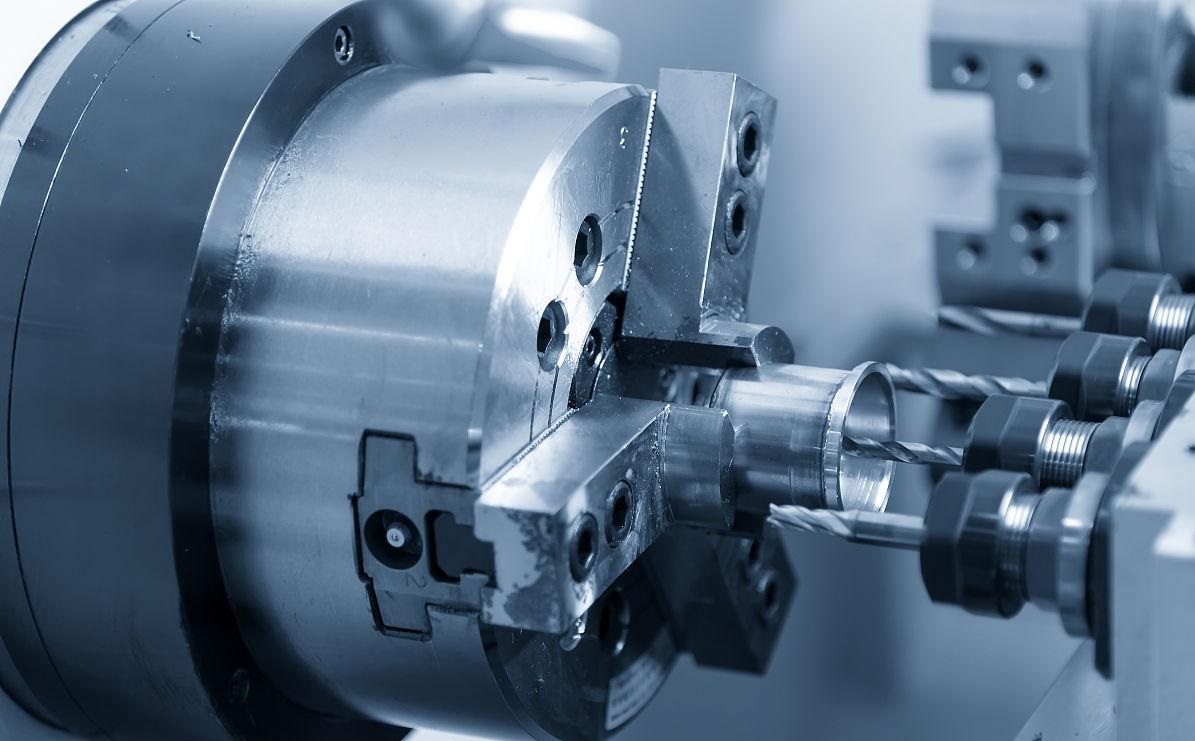
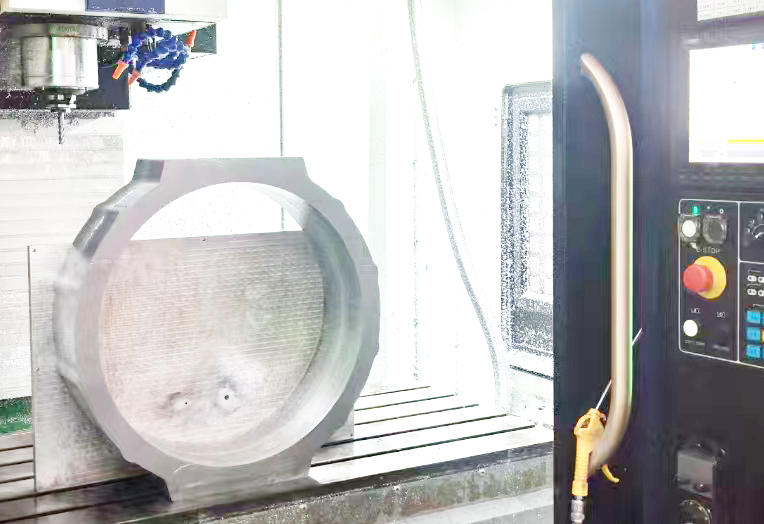
How CNC Machine Setups Impact Your Project Budget?
Understanding the Cost Drivers of CNC Setups
Depending on the design complexity, CNC operators might need multiple setups to fully machine a part, especially when the part features multiple surfaces or intricate geometries. Each time a part needs to be repositioned, recalibrated, or moved between machines, additional time and costs are incurred. This setup time can quickly add up, particularly in more complex machining scenarios.
For instance, a part that only needs one setup on a 3-axis machine will cost less compared to a part requiring multiple setups to access different faces or features. The complexity of the design and the access required for the tools play a significant role in determining setup requirements.
Key cost drivers in CNC setups include:
- Fixturing: Ensuring that the part stays securely in place is critical for both accuracy and efficiency. While standard vices may work for some parts, others with irregular shapes may require custom fixtures, which take time to design and fabricate, thus adding to the overall cost.
- Specialized Tools: If your design involves unique features, special tools might be necessary. These tools can range in price from $50 to $500, and for low-volume production, this cost per part can rise significantly.
- Toolpaths: Optimized toolpaths are vital for reducing machining time. Inefficient toolpaths result in longer machine times, driving up both time and cost.
How Multiple Setups Influence Costs
The more CNC setups involved, the greater the time spent on resetting machines, recalibrating tools, and adjusting fixtures—all of which add to the cost. Additionally, factors such as the material choice (especially if using tough or exotic materials) and non-standard tools can further inflate project expenses.
While there's no fixed cost to the number of setups, the general rule is: more setups = higher costs. Also, remember that materials that are harder to machine, such as exotic alloys, not only increase the setup complexity but also lengthen production times, making your project more costly.
Optimizing for Cost Efficiency
To keep CNC machining projects cost-effective, consider the following strategies:
- Increase Production Run: Ordering a larger batch can spread the costs of tooling, fixtures, and setup over more units, effectively lowering the cost per part.
- Choose Cost-Effective Materials: Standard materials like aluminum or low-carbon steel are easier and faster to machine, reducing both material and machining costs. Exotic materials, on the other hand, can significantly increase costs due to the need for specialized tools and slower machining times.
- Leverage Standard Tooling and Fixtures: Standard sizes and materials will save you the cost of custom designs. Custom fixtures, while sometimes necessary, should be minimized as they increase both lead time and cost.
- Don’t Over-Tolerate: Tight tolerances often require more time and precision, which can extend machining hours and lead to higher costs. Unless absolutely necessary for the functionality of your part, opt for more lenient tolerances.
- Conduct DFM Early: Design for Manufacturing (DFM) checks can help catch potential issues early, such as deep pockets or sharp internal corners, which require more specialized tools. By identifying these problems early, you can adjust your design to be more cost-effective.
By optimizing your design, material choice, and setup process, you can significantly reduce your CNC machining costs without compromising on quality.