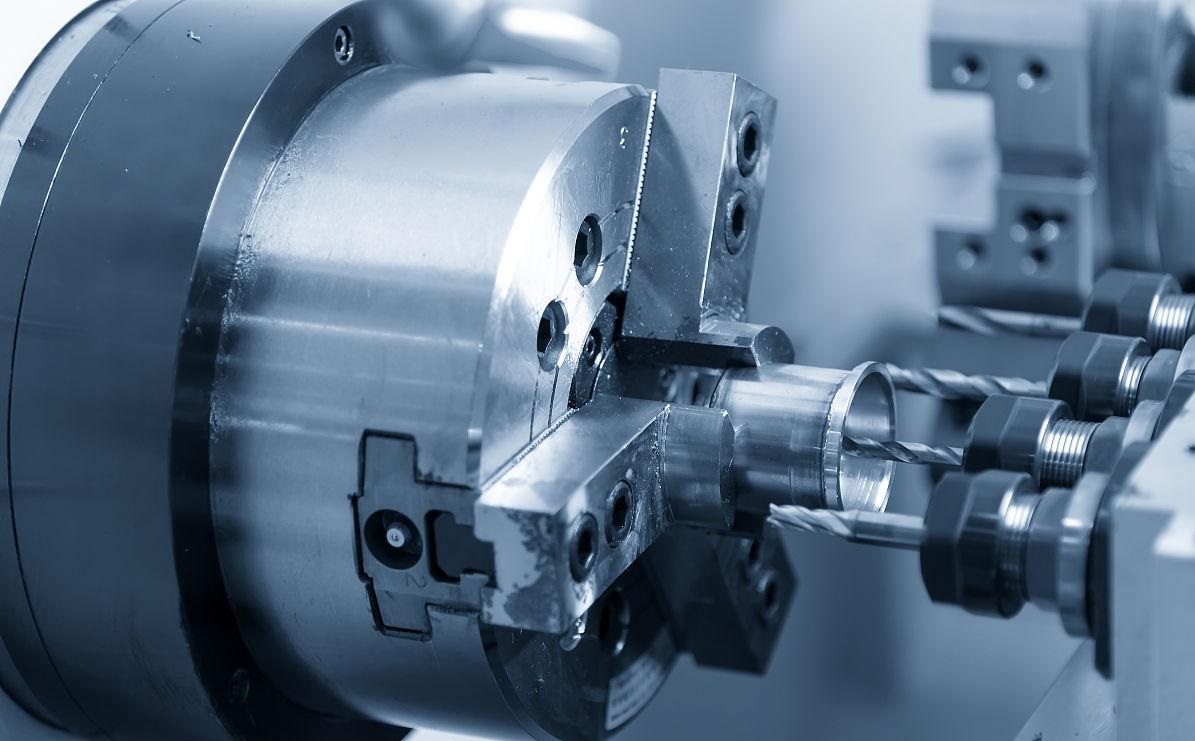
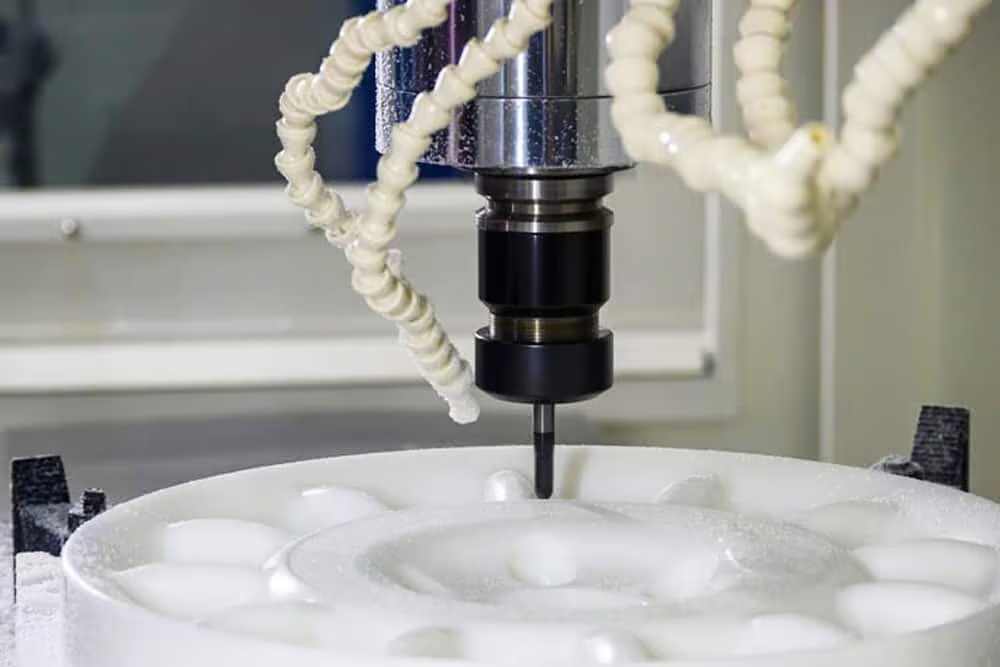
What Are the Best Methods for Deburring After CNC Machining?
Deburring is a crucial post-machining operation that smooths out these rough edges, ensuring your components meet high-quality standards. Not only does it improve the appearance of the part, but it also enhances its performance by eliminating sharp edges that could cause damage during use or assembly.
In this article, we'll explore what deburring is, why it's important, and the best methods to effectively deburr your parts after the CNC machining process.
What is Deburring?
Simply put, deburring is the process of removing burrs—those tiny, jagged edges left on the surface of a part after cutting, milling, or turning operations. These burrs can cause a range of problems, from poor aesthetics to functional issues. Whether it's a sharp edge that can cause injury or an uneven surface that can affect the fit of parts, deburring is essential for the final quality check.
Why is Deburring Important?
While burrs may seem like a minor concern, they can significantly affect the integrity and usability of your parts. Not only do burrs impact the part’s appearance, but they also affect assembly, safety, and durability. Sharp edges can damage other components or even cause injuries. In industries like aerospace, medical, or automotive, where precision is critical, deburring ensures that parts function as intended without compromising safety or performance.
Methods for Deburring After CNC Machining
Vibratory Finishing Vibratory finishing uses a vibrating tub or bowl where parts, abrasive media, and compounds are placed. As the parts vibrate, they rub against the media, effectively removing burrs. This method is ideal for deburring in bulk, providing consistent results and can be used for polishing, cleaning, and surface preparation as well.
Barrel Tumbling Barrel tumbling works by placing parts, abrasive media, and compounds in a rotating barrel. The media's friction helps wear down the burrs, smoothing out the edges. It’s a cost-effective option for parts that require a more aggressive deburring process, and it’s excellent for achieving uniform results. It's especially useful for high-volume production.
Manual Deburring Manual deburring involves using hand tools like files, brushes, or rotary tools to remove burrs. While this method can be labor-intensive and time-consuming, it’s ideal for small batches or delicate parts that require a more controlled approach.
Abrasive Blasting Abrasive blasting involves propelling abrasive media (like sand or glass beads) at the part's surface to remove burrs and smooth out rough areas. This method is fast and effective, especially for parts with intricate shapes or tight tolerances. However, it may require additional cleaning to ensure no media is left behind.
Electrochemical Deburring (ECD) ECD uses an electrochemical process to remove burrs without physically contacting the part. This method is ideal for hard-to-reach areas or intricate geometries, making it an excellent choice for complex parts with tight tolerances.
Conclusion
Deburring is a critical step in the CNC machining process that ensures the functionality, safety, and aesthetics of your parts. Whether you choose vibratory finishing, barrel tumbling, or another method, removing burrs is essential to delivering high-quality, precision components. Select the deburring method that best suits your production needs to enhance the efficiency and performance of your CNC machining operations.
By mastering the deburring process, you’ll achieve superior results and maintain the highest standards in your machining projects.