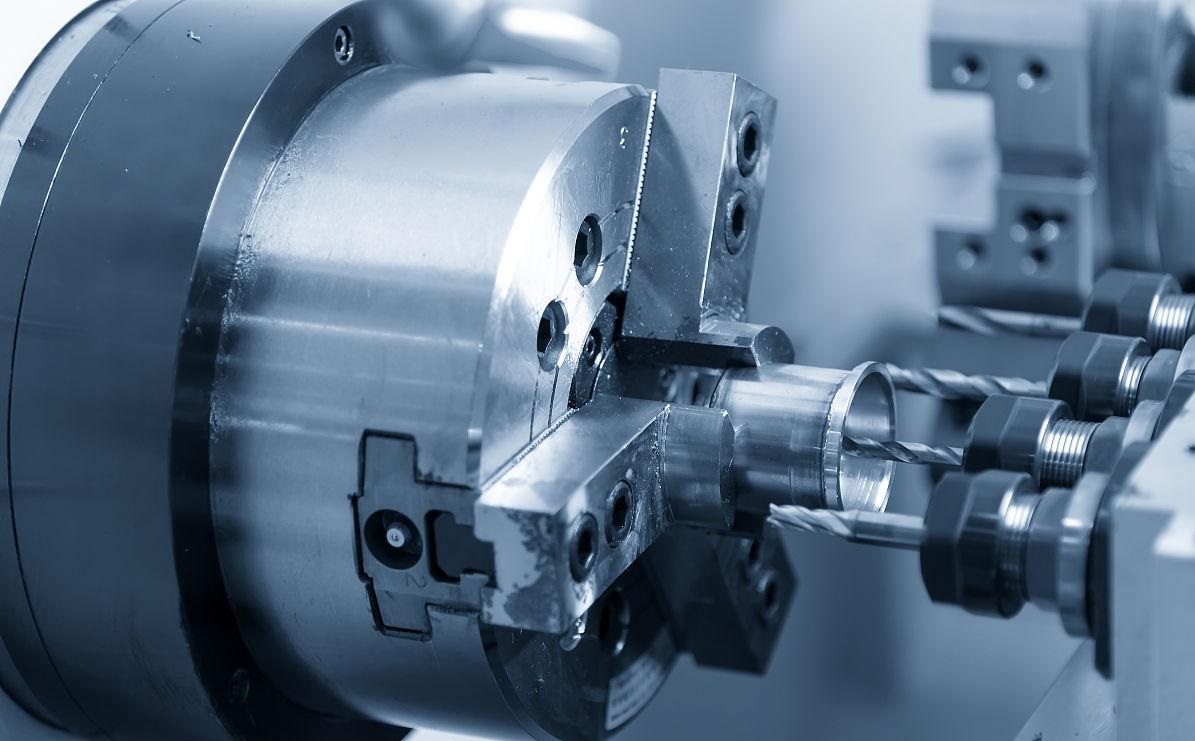
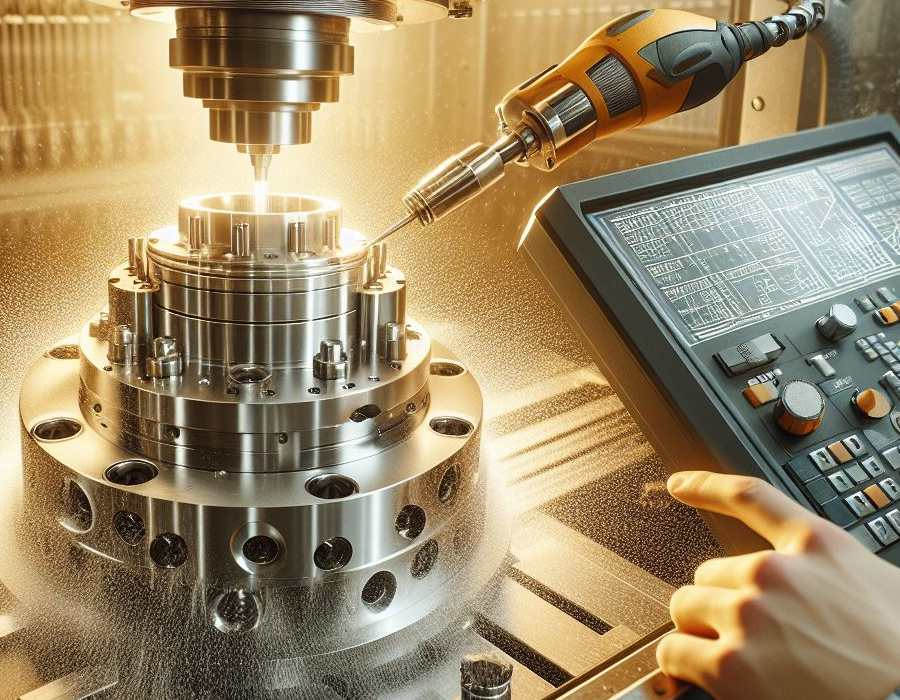
How to Maximize Your CNC Machining Capabilities Without Raising Costs?
Expanding CNC machining capabilities is crucial for staying competitive and meeting the increasing demand for precision parts. However, growth often comes with concerns about rising overhead and labor costs. Fortunately, there are strategic approaches to enhance production capacity efficiently without significant expense. This article explores key strategies to optimize CNC machining operations while keeping costs under control.
1. Utilize Automation for Efficiency Gains
Automation is a powerful tool for expanding machining capacity without increasing labor costs. By integrating automated systems, manufacturers can enhance productivity and consistency.
Automated Material Handling – Robotic arms and conveyors reduce manual intervention, speeding up production and minimizing errors.
CNC Tool Automation – Automatic tool changers (ATC) allow seamless tool switching, minimizing downtime and improving machine utilization.
Automated Quality Control – Machine vision systems and automated inspection tools streamline quality checks, reducing reliance on manual inspection.
Implementing automation boosts throughput, improves precision, and ensures round-the-clock operation without additional labor expenses.
2. Optimize Machine Utilization with Smart Scheduling
Effective scheduling ensures maximum output from existing machines without requiring additional investment.
Shift Optimization – Running machines during off-peak hours or implementing multiple shifts increases productivity without adding new equipment.
Job Prioritization – Smart scheduling software helps prioritize jobs based on urgency and resource allocation, ensuring efficient machine usage.
Preventive Maintenance – Regular maintenance prevents breakdowns, reducing costly downtimes and keeping machines operating at peak efficiency.
By refining scheduling and maintenance, manufacturers can maximize capacity without inflating overhead costs.
3. Outsource Non-Core Operations
Outsourcing secondary operations allows manufacturers to focus on high-value machining tasks without overloading resources.
Subcontract Finishing Services – Processes like plating, heat treating, and coating can be outsourced to specialized providers, freeing up in-house machining capacity.
Specialized Machining Partnerships – Partnering with subcontractors for complex materials or intricate geometries eliminates the need for costly equipment investments.
Strategic outsourcing ensures flexibility and expands capabilities without the burden of additional machinery or labor costs.
4. Leverage Additive Manufacturing for Prototyping and Tooling
Additive manufacturing (3D printing) is an efficient way to expand capabilities, especially for rapid prototyping and tooling needs.
Prototyping Efficiency – 3D printing speeds up design iteration and reduces material waste compared to traditional machining methods.
Custom Tooling and Fixtures – Printed jigs and fixtures can enhance CNC operations, lowering tooling costs and improving workflow efficiency.
Incorporating 3D printing streamlines development processes while reducing lead times and material costs.
5. Invest in Multi-Function CNC Machines
Multi-function CNC machines combine multiple machining processes into a single setup, reducing reliance on multiple machines and operators.
Mill-Turn Machines – These hybrid machines integrate milling and turning operations, minimizing setup changes and increasing machining efficiency.
Swiss-Type Lathes – Ideal for high-precision small parts, Swiss lathes perform multiple operations in a single cycle, reducing handling time and errors.
Investing in versatile CNC machines enhances efficiency and broadens machining capabilities without excessive equipment costs.
6. Enhance Workforce Skills for Maximum Productivity
A well-trained workforce is key to optimizing machining operations without adding more personnel.
Cross-Training Employees – Training operators on multiple machines ensures workforce flexibility and efficient resource allocation.
Advanced CNC Training – Providing continuous education on programming, process optimization, and troubleshooting improves overall operational efficiency.
Empowering employees with the right skills enhances productivity, reducing errors and machine downtime.
7. Apply Lean Manufacturing Principles
Implementing lean manufacturing strategies helps eliminate inefficiencies and maximizes existing resources.
Process Optimization – Identifying bottlenecks and streamlining workflows reduces waste and enhances production speed.
Inventory Control – Effective inventory management prevents material shortages and minimizes excess stock costs.
Continuous Improvement (Kaizen) – Encouraging a culture of ongoing improvements leads to sustained efficiency gains over time.
Lean principles ensure smoother operations and expanded machining capabilities without unnecessary expenses.
Conclusion
Expanding CNC machining capabilities does not have to mean increased overhead or labor costs. By leveraging automation, optimizing machine utilization, outsourcing non-core operations, and investing in multi-function machines, manufacturers can enhance efficiency without major capital investment. Additionally, adopting additive manufacturing, upskilling employees, and applying lean manufacturing strategies further drive growth while maintaining cost control. With smart planning and continuous process improvement, CNC shops can scale operations effectively and profitably.