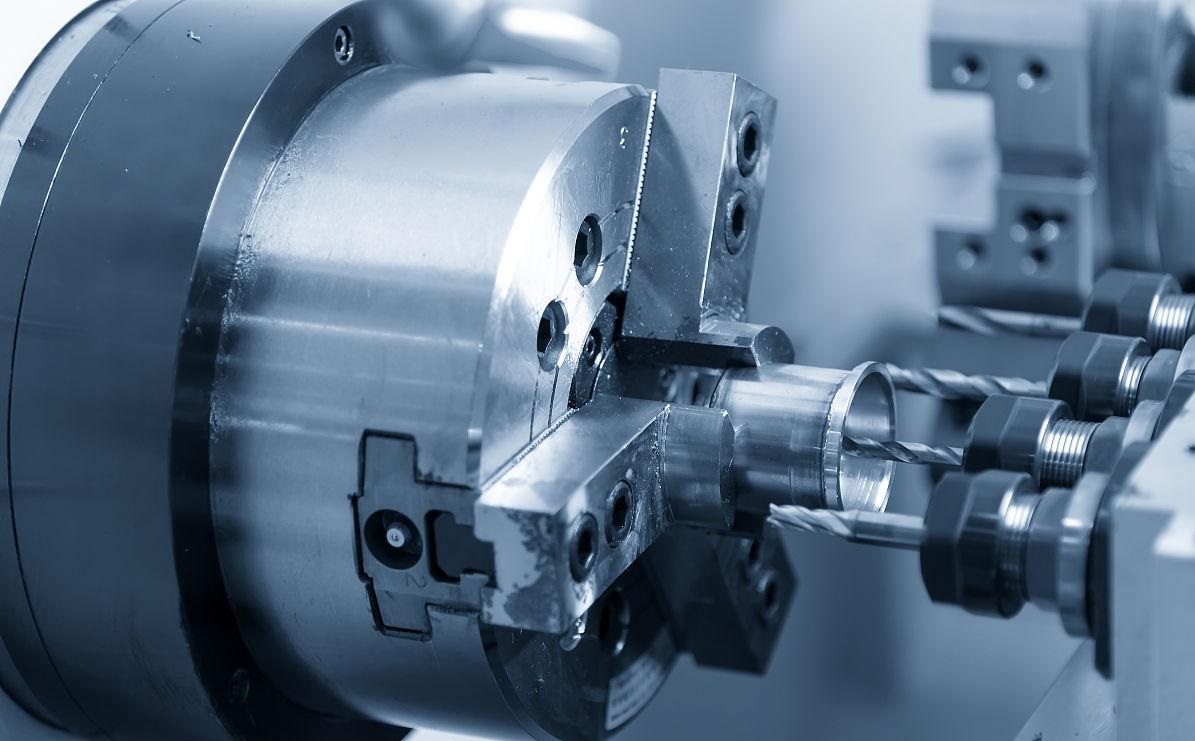
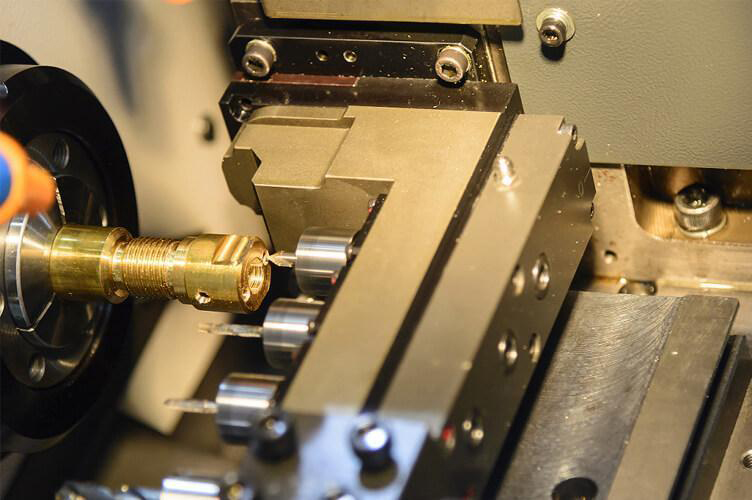
Why Is Brass a Go-To Choice for CNC Machining?
Brass is one of the most widely used materials in CNC machining, offering an exceptional combination of machinability, durability, and aesthetic appeal. But what exactly makes brass so suitable for precision machining? Let’s break down the key properties that make this metal an excellent choice for CNC manufacturing.
Key Properties of Brass
Property | Brass |
---|---|
Melting Point | 885 to 890 ℃ |
Density | 8.5 g/cm³ |
Modulus of Elasticity | 97 GPa |
Thermal Conductivity | 115 W/m-k |
Electrical Resistivity | 6.3×10⁻⁸Ω |
The specific characteristics of brass depend on its composition, mainly a blend of copper and zinc, sometimes with trace amounts of magnesium, silicon, iron, or lead. These additional elements impact the grade and properties of the alloy, enhancing its performance in different machining applications.
Why Brass Excels in CNC Machining
Superior Electrical and Thermal Conductivity
Brass, rich in copper content, is highly conductive, making it ideal for applications requiring efficient heat and electricity transfer. This property makes it particularly suitable for electrical components such as connectors, terminals, and heat sinks. Additionally, its high thermal conductivity enables efficient machining, particularly in Electrical Discharge Machining (EDM), reducing cycle times and production costs.
Excellent Corrosion Resistance
One of the key advantages of brass is its ability to withstand corrosion. The level of corrosion resistance depends on the alloy composition—higher aluminum content enhances resistance, while increased iron content may reduce it. This characteristic ensures that brass parts have a longer lifespan, even in high-moisture environments, making them ideal for marine, plumbing, and industrial applications.
High Malleability for Complex Designs
Brass is highly malleable, allowing it to be easily formed into intricate shapes without cracking. This makes it an excellent choice for custom CNC parts, especially those requiring detailed designs and tight tolerances. The metal’s malleability is primarily attributed to its copper content—higher copper levels result in even greater workability.
Strength and Hardness for Durability
Although brass is not as hard as some steel alloys, it is still strong enough for many structural applications. The presence of aluminum in certain brass grades enhances its hardness by forming a protective aluminum oxide layer, increasing wear resistance. This makes brass a reliable choice for parts that require durability without sacrificing ease of machining.
Exceptional Machinability
One of brass’s standout features is its excellent machinability. The presence of lead in certain brass alloys enhances its ductility, reducing tool wear and ensuring smooth, precise cuts. Machinists favor brass because it allows for faster processing speeds, reducing overall machining time and costs. This property makes brass a top contender for high-precision, high-volume CNC projects.
Aesthetic Versatility
Brass doesn’t just perform well—it looks great too. With its natural range of colors, from reddish-gold to bright gold or even silvery tones, brass is often chosen for decorative applications. The alloy’s final appearance depends on its copper-to-zinc ratio, allowing manufacturers to achieve a variety of finishes without additional surface treatments.
Conclusion
Brass is an outstanding material for CNC machining due to its excellent machinability, corrosion resistance, malleability, strength, and aesthetic versatility. Whether you’re manufacturing precision components for the electrical, marine, or decorative industries, brass offers a cost-effective, durable, and high-performing solution. Its ability to deliver high-quality results with minimal machining effort makes it a favorite among manufacturers worldwide.