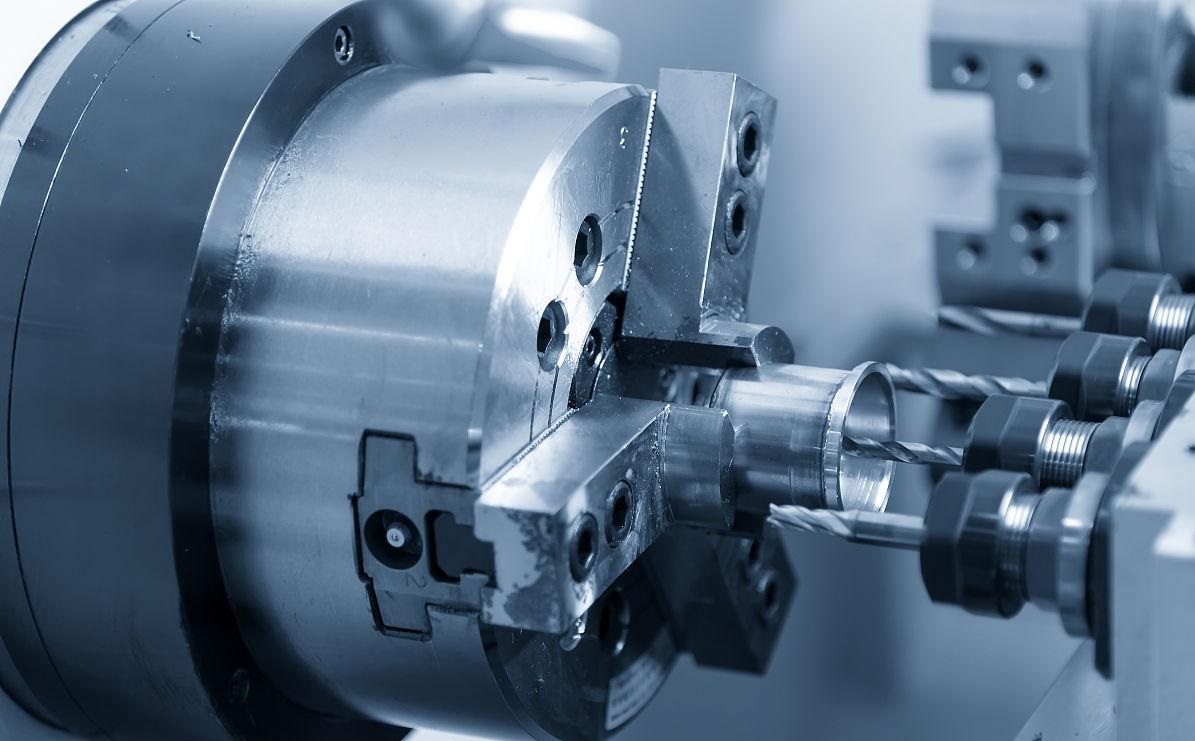
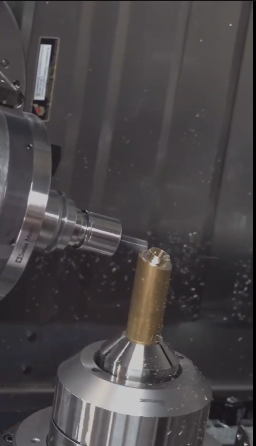
How to Prevent Deformation in CNC Machined Metal Parts: 5 Practical Tips You Shouldn’t Ignore
In CNC machining, producing precision metal parts is the goal—but part deformation is a silent challenge that can disrupt production, delay delivery, and increase cost. Even strong metals like aluminum or stainless steel can warp or distort under the pressure of cutting tools and heat.
If you’ve ever faced unexpected shape changes during or after CNC machining, this article is for you.
We’ll walk you through what causes metal deformation in CNC processes and offer five actionable ways to minimize or prevent it—so you can deliver high-quality parts, every time.
Why Does Metal Deformation Happen in CNC Machining?
Although metals are known for their durability, they can still deform under certain machining conditions. Deformation typically occurs due to mechanical stress, thermal influence, or improper fixturing. Here are the main reasons:
1. Material Properties and Part Geometry
Softer metals, such as aluminum or copper, deform more easily than harder ones. Parts with thin walls, complex geometries, or sharp transitions are more susceptible to bending or warping during machining.
2. Residual Internal Stress
Internal stress from casting, rolling, or heat treatment may be released during cutting. This can cause the material to shift unpredictably once machining begins.
3. Improper Clamping or Fixturing
If the workpiece isn’t securely clamped—or if the clamping force is uneven—it may shift during machining or spring back after being released.
4. Incorrect Tooling or Feedrates
Worn tools, aggressive cutting speeds, and high feedrates can introduce excessive forces, increasing heat and vibration that lead to deformation.
5 Tips to Avoid Deformation During CNC Machining
Let’s look at how you can address the causes mentioned above with smart solutions:
✅ 1. Reduce Internal Stress Before Machining
One major source of deformation is residual stress in the material. To mitigate this:
Use pre-machining heat treatments like annealing to relax the internal stress.
Consider stress-relief processes such as shot peening or natural aging, especially for aluminum alloys.
After machining, apply stress-relief again if high-precision is required.
✅ 2. Use the Right Cutting Tools and Techniques
Tool selection plays a vital role:
Choose sharp, rigid tools made from high-performance materials.
Apply coolants during cutting to reduce heat buildup and avoid thermal expansion.
Avoid deep cuts in a single pass. Multiple shallow passes can reduce stress on the part.
Regular inspection and maintenance of tools prevent vibration and uneven loads that may lead to unwanted movement.
✅ 3. Optimize the Clamping Method
Proper fixturing minimizes movement:
Use evenly distributed clamping pressure across the workpiece.
Support fragile areas and avoid over-tightening.
For thin or flexible parts, vacuum fixtures, soft jaws, or custom clamps may offer better results than standard vises.
Clamping should not induce stress itself—ensure the setup allows for minimal deflection during cutting.
✅ 4. Design for Machinability
Good part design reduces the chance of deformation:
Avoid sharp internal corners or ultra-thin walls.
Make symmetrical designs where possible.
Adjust tolerances wisely—don't apply tight tolerances where they're not functionally needed.
Working closely with your machinist during the design stage can help you foresee potential deformation risks.
✅ 5. Optimize the Production Process
Several other parameters also play a role:
Coolant type and flow rate must be selected for the material. Improper cooling leads to thermal stress.
Feedrate and cutting speed should be adjusted based on material hardness and part geometry.
For low-volume or highly complex parts, consider rapid prototyping for validation before final machining.
Don’t forget: modern simulation tools can help anticipate material behavior during machining.
Conclusion
Avoiding deformation in CNC machined metal parts is not a one-time fix—it requires a thoughtful combination of correct material preparation, optimized cutting strategy, proper fixturing, and smart design.
By following the five tips outlined above, you can greatly reduce deformation, save on production costs, and achieve high-quality results consistently.
Whether you're producing aerospace components, automotive brackets, or medical housings, controlling deformation is key to precision and performance.
🔧 Need help with custom metal parts that hold their shape and function? Our team at Pincheng is here to support your next project.
📩 Contact us today to learn more.